Mic TechNiche is a random blog series, updated on a whenever-I-feel-like-it basis, where we try to de-mystify some of the goings-on of microphones, from marketing hypewords to circuit topologies to an inside peek at our process. TRIGGER WARNING: may contain dad jokes and stale pop culture references.
What’s WIMA?
One oft-touted marketing line of roughly one million microphone manufacturers is “WIMA caps”. You’ll see this from basically every price point on the market. I recently had someone ask me on our Instagram messages “do you guys use WIMA caps? What does that mean for the sound of the mic?” The answer is – it’s complicated. So let’s dive in.
WIMA (technically “WIMA Spezialvertrieb elektronischer Bauelemente GmbH & Co.KG”…but let’s just go with WIMA) is a highly-regarded German capacitor manufacturer. They’ve been building fantastic capacitors for various applications since 1948 in a very distinct “box” style. If you peek inside a vintage European-made mics, there’s a good chance you’ll spot some WIMA capacitors hanging out in there.
But before we get to deep into why WIMA does or doesn’t matter – let’s get a quick-and-dirty (and oversimplified!) primer on what capacitors do in microphone circuits.
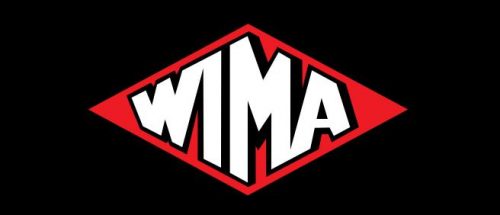
“A WIMA WIMA WIMA, A WIMA WIMA WANG!” -Linda Belcher, activist
Talk Nerdy To Me
A capacitor is a very common electronic component that’s in darn near every circuit in your house. Your phone, your car radio, your computer, your TV, your TV remote…all of them have capacitors performing various functions within the circuit. Very simply, a capacitor’s unique function is in it’s name – it has the capacity (see?) to store electrical energy.
[SIDEBAR TIME! Capacitors originally were called “Condensers” or “Condensators”. That is almost entirely obsolete language, except in one place – microphones! A condenser capsule essentially functions as a special kind of capacitor…that’s why you’ll sometimes see condenser microphones referred to a “capacitor microphones”. Or for a few German (or pretending-to-be-German-look-how-totally-German-we-are-guys) mic companies, “Kondensator” or “Kondensor” microphones.]
In audio, capacitors have a neat & helpful trick – they block DC (direct current) while allowing AC (alternating current) to pass. The electrical representation of sound in a circuit is AC, so capacitors “let sound through” in a circuit – an oversimplification, but accurate for our purposes here. DC is important to power parts of the head-amp circuit in your condenser microphone – it gives transistors, tubes, and other sections the energy required to make the mic work. But, for a lot of reasons, DC is really not good to have heading down the cable to your preamp.
So capacitors typically get put in the middle of the audio path in a microphone as “decoupling” capacitors – they are blocking the DC from getting to your XLR cable and containing it to the areas where it needs to be, but they’re allowing the AC audio signal to go on through. They’re basically a better version of the crossing guard that always makes me wait 3 lights before I can get to the office.
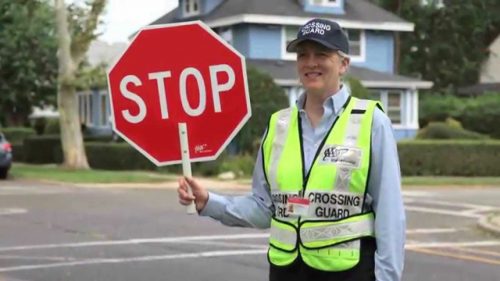
Seriously, Barbara. They made it across like 30 seconds ago…Get out of the way.
Now in theory, a capacitor that sees an AC signal on one side will pass that exact AC signal over on the other side. But while a capacitor is a better crossing guard than Barbara, it’s not a perfect one. In the real world, capacitors affect the audio signal in some way. They might introduce distortion, they might not pass the different frequencies through equally, they might have less-than-ideal leakage or absorption (gross). They’re basically imparting some of their “personality” on the signal, in the same way that your compressor, EQ, microphone, or preamp might.
There’s a LOT of different factors that go into what that personality is. The physical way the capacitor is constructed, the materials in the capacitor, the size, whether the capacitor’s mom said “I love you” enough…these are just a few parts of that equation. If you go on Mouser.com (a big electronics vendor) they have nearly 500,000 different capacitors in their lineup. That’s a LOT of variety, and variety is the spice of life. Or, in our case, microphones.
A lot of really inexpensive mics use the cheapest possible capacitors that have straight-up terrible characteristics for passing a good-quality audio signal. They might cause distortion, or have really poor performance at certain frequencies. There’s even certain capacitors that have an excess of piezoelectric effect – essentially, they pick up mechanical vibrations (i.e. sound waves) and insert it into the signal!
So if you have a crappy capacitor that doesn’t do a great job at passing that signal down the line without borking it up somehow…you’re gonna have a bad time.
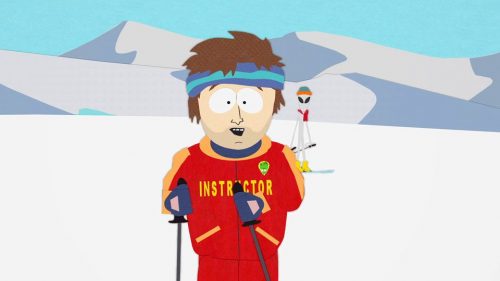
Thanks, Thumper
So…are WIMA caps good?
So now that we’re through that…back to WIMA. Are they better at passing audio signals than other capacitor brands?
I don’t want to repeat myself, but…it’s complicated! WIMA caps can be a fantastic choice for audio. But that depends ENTIRELY on the type of WIMA capacitor, where and how you’re using it, and a number of other factors.
#1: Audio is subjective, and relative to the situation. Ok, engineer/producer guy who probably hasn’t read this far – let’s try an analogy. you’ve got a compressor that does a great job getting that smashed, pump-y sound. On a parallel drum buss in a rock (RAWK!) track, that compressor might be a total eargasm. On a symphony piece with an orchestra, probably not something you’re reaching for, right? I don’t think Tchaikovsky would be down with CLA-style drum compression on the strings in The Nutcracker Suite.
The subjective audio qualities of the capacitor you choose are just as situational. If I’ve got a really bright, zippy K67-style capsule in my mic with a circuit that doesn’t compensate for its peppy demeanor, a capacitor that has a “smoothing” sound to the top end is probably really useful. Maybe not so much on a mic that already has a “darker” top end. It’s important to choose a cap that works in tandem with the rest of the circuit, in the same way that Tchaikovsky will come back from the dead and murder you if you start pumping his piano Concerto with an 1176.
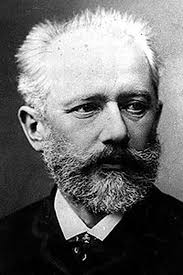
Anyone with sideburns like this is NOT to be trifled with.
#2: WIMA makes a bunch of different types of capacitors that are suited for different tasks. The dielectric material is REALLY important in regards to the tonal characteristics of a capacitor for audio applications. Some manufacturers choose the lowest-cost one, and *Coach Steve Spoiler Alert!* it doesn’t sound very good in the audio path. Just because it’s WIMA doesn’t mean it’s supposed to be a good audio-application capacitor!
More detail: the least expensive WIMAs are their MKS series. MKS caps use metallized polyester film (“PET”) as the dielectric material for the capacitor. If you’re looking for them on your circuitboard, look for a red box with a red epoxy filler on the bottom and white or silver text.
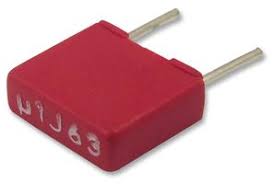
A WIMA MKS2 capacitor, with a value of 0.1uF and a 63V DC rating.
This is just my opinion, but I’ve actually heard far better PET capacitors than WIMAs when it comes to signal path applications. In general, PET caps tend to introduce a grainy quality, as they add more distortion than other dielectrics. If you see red WIMA box capacitors with white or silver text in your mic nearer to the XLR connector than the capsule, my personal opinion is this – NO! I personally have a preferred brand for PET caps when I have to use them in microphones, and WIMA is not it. I’ve even preferred unbranded generic “chiclet-style” PET caps when I’ve tested them against WIMA MKS.
It’s nothing against MKS caps…they’re just ill-suited for the particular task of the audio signal path. I’ve used WIMA MKS caps in power sections of microphone circuits with quite a bit of success when I need high, tight-tolerance capacitance in a small size. [One great thing about metallized PET is you can get high, precise values in a really small footprint when compared to other film dielectrics].
I’ve seen WIMA MKS capacitors in the signal path in some very low-cost OEM mics out of China, and I’ve seen them (unfortunately) in pretty high-priced microphones too. But when I saw that back in the day, I always knew I had an easy mod for a client that would really make a difference. Subbing them out for a more suitable series of WIMA capacitor, or even a different brand of PET film cap, gives you a solid uptick in sound quality right away. But here’s the kicker – it’s also more expensive…and THIS is where you can see where a microphone manufacturer’s intentions lie.
We’re talking mere nickels in terms of the difference in cost between WIMA MKS capacitors and much more suitable signal path WIMAs. When someone is more concerned with shaving down costs than bang-for-your-buck performance increases (or they just don’t know any better)…well, they might throw in MKS caps for the “name drop” value of WIMA caps in their mic…and then fail to mention that they’re using the worst-suited audio-path WIMA capacitors.
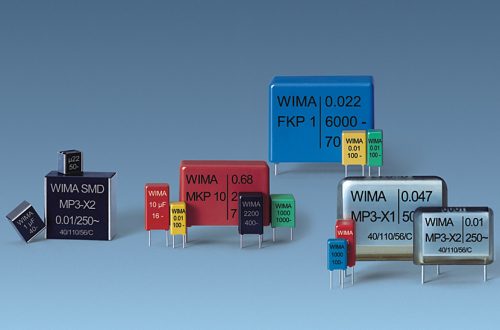
These are all WIMA capacitors with various material and construction styles for different applications. Those old green Miflex caps are quite lovely for capsule-to-grid/capsule-to-gate decoupling if you can find them!
#3: There’s other brands besides WIMA that make really great signal path capacitors too. Small-sized “box”-style capacitors with higher-quality dielectrics are quite abundant. We use capacitors from a number of manufacturers, including WIMA, in our microphones. In R&D, we’ll use two different brands of capacitor with identical specifications – capacitance, voltage rating, dielectric, construction style – and they will sound WAY different. Yet on paper, the caps are practically identical except for the brand!
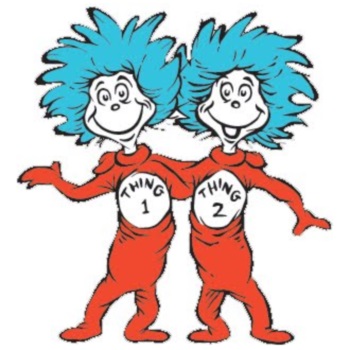
Thing 1 and Thing 2 – supposedly the same, but I’ve always had a sneaking suspicion that Thing 2 is a smarmy git
That’s part of why we’ll test 20+ capacitors in the exact same critical signal-path location…it makes a BIG difference in the final sound of our mics. Sometimes the final choice is a really nice expensive PP-and-foil cap. Other times, it can be the oddball electrolytic I threw in as an afterthought. Is it a lot of work? Absolutely. Does it make our microphones 1%, 5%, or sometimes 20% better when we find “the one” after hours of listening? Absolutely.
Making a microphone is a lot like making a recipe. There’s so many permutations within, for example, grilling a steak: the amount, type, and quality of the seasonings; the cut & thickness of the meat; the temperature of the grill; propane or charcoal…and these are off the top of my head. In a microphone, there might be several capacitors in the signal path at various stages of the circuit. Each of these imparts its own character on the microphone. I might find that a particular WIMA capacitor is fantastic as a pre-transformer signal path capacitor in one microphone, but in another microphone it doesn’t quite hit the mark. That’s where I might try a different style of WIMA, or a different brand…or something else! There’s half a million capacitors on Mouser, remember? I’ve barely scratched the surface. I’m always looking for the “next one” that no one has tried yet.
The Conclusion (FINALLY!)
So we’re back to #1, and it’s becoming a mantra at this point: Audio. Is. Subjective. The most important test of any microphone is not the brand of capacitor, or the place of manufacture, or the FR chart. It’s YOUR EARS. That’s why we develop our mics in studios, on real sessions, in front of real instruments. There is no substitute in for listening, taking notes, adjusting, and listening some more. It takes a long time…but it’s worth every single minute. The development cycle average of each of our mics is probably hovering around 3 years (and if you count when we first put pen to paper for certain ideas, we’re talking 10+ years). I’m always going down the rabbit hole of “what if we tried THIS combination?!?”. It’s my version of some ridiculous obsession, like collecting vintage milk bottles.
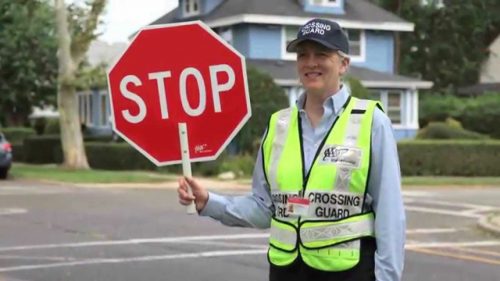
20 bucks says that’s Barbara’s dumb hobby
So TL;DR version: higher-quality (and higher-cost!) WIMA capacitors are an excellent option within a microphone’s signal path. But for the low-cost WIMA MKS caps, not so. Whenever you see “WIMA film caps” in marketing material, be aware that it’s not the entire story.
Thanks for reading (if you got this far!). if you have any questions, or feedback, or would like to discuss what cookies go best with eggnog, email me at derek@vanguardaudiolabs.com. And if you want to use your ears to check out our mics, stay tuned for our risk-free USA demo program or check out our SoundCloud listening station!